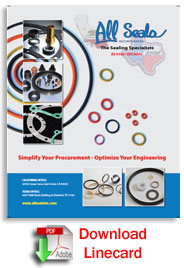
All Seals Incorporated
The Sealing Specialists
CALIFORNIA OFFICE:
20762 Linear Lane
Lake Forest, CA 92630
Phone: (714) 556-4931
Toll Free: (800) 553-5054
Fax: (714) 557-3257
TEXAS OFFICE:
4407 Halik Road, Building A
Pearland, TX 77581
Phone: (281) 404-4384
Toll Free: (800) 553-5054
Fax: (281) 715-5379
|
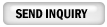 |
|
Types of Rubber and Basic Properties |
|
Key: E = Excellent G = Good F = Fair P = Poor
The information given above is only an indication of the properties achievable for the range of elastomers listed. All Seals offers no guarantees on the suitability of its products for a particular set of conditions based upon the contents of this table.
Click below to download Material Selection - Fluid Compatibility Chart
Select a chemical name from the list. You may either use the search box
when open Adobe Acrobat or choose from the alphabetical fluid names.
Durometer is the international standard for measuring the hardness of rubber, plastic, and most nonmetallic materials. The hardness of a material is its resistance to surface penetration. Harder materials have more wear resistance, but they are also less flexible. Note that an object may fall within more than one scale. For example, a typical shoe heel is 95 Shore OO, 70 Shore A, and 22 Shore D durometer.
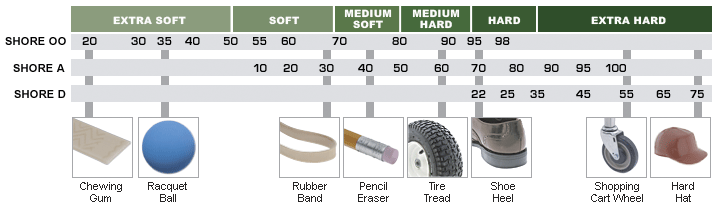
|
|
Aflas® or TFE/P is a member of a new generation of fluoroelastomers compounded especially to provide unique properties for specific applications. The primary uses for Aflas are in parts for oil drilling equipment. Aflas can be crosslinked (cured) using a variety of systems, but generally peroxides are used to provide the best all around environmental resistance. A unique property of TFE/P is, that at very low temperatures (down to -54 °C) it takes on leathery consistency and remains functional, unlike many other rubbers which can often become brittle and shatter at low temperatures.

|
|
Butyl, also known as Isobutylene-isoprene (IIR), is a synthetic rubber developed in the 1940’s. It has exceptionally low gas permeability making it ideal for inner tubes and high pressure/vacuum sealing applications. Its very low resilience makes it suitable for shock and vibration damping. Its chemical unsaturation gives it excellent resistance to heat, ozone, and weathering, and also to dilute acids and alkalis.
It is not suitable for use in mineral or petroleum based fluids.
Typical applications include diaphragms, gaskets, inner tubes, liners, O-rings, seals, speaker surrounds and bottle closures.

|
|
Chlorosulphonated Polyethylene (CSM), widely known as Hypalon®, can in some respects be regarded as a superior type of chloroprene, having better heat ageing, chemical resistance and excellent low gas permeability. Ozone and weathering resistance is also excellent and electrical properties are good. Low temperature flexibility and oil resistance is similar to chloroprene.
Hypalon has poor fuel resistance and dynamic sealing applications are not recommended in view of its poor compression set.
Typical applications include static seals and any components likely to suffer hot and humid weather conditions or exposure to hot liquids and gases. |
|
Epichlorohydrin (ECO) has properties similar to nitrile rubber but with better heat, oil and petrol resistance. It has a low gas permeability and better low temperature flexibility than NBR. Its resistance to acids, alkalis and ozone is excellent.
However, its poor compression set limits its use as a sealing material and its corrosive effect on metals can increase tooling costs and limit metal bonding applications.
Typical uses are in automotive fuel systems, bladders, diaphragms and rollers. |
|
Ethlylene Propylene Diene Monomer is a copolymer of ethylene and propylene and a smaller amount of a diene monomer which forms chemically unsaturated ethylene groups pendant from the main saturated chain. These facilitate cross-linking reactions which do not affect the integrity of the polymer backbone. This feature gives EPDM excellent heat, ozone and chemical resistance. Physical properties are very good and resistance to polar fluids is generally good. Low temperature resistance is very good and EPDM can be compounded to give excellent electrical resistance.
EPDM is not suitable for exposure to petroleum based fluids and di-ester lubricants.
Typical applications include accumulator bladders, cable connectors and insulators, diaphragms, gaskets, hoses and seals.
Potable water (WRC/WRAS) grades are available as well as ‘Food Quality’ mixes suitable for the food and pharmaceutical industries.

|
|
Fluoroelastomers or Fluorocarbons, widely known as Viton®, are among the most suitable rubbers for continuous use at temperatures of 200°C and up to 300°C for short periods. Various grades are available depending upon whether compression set, flexibility (as in diaphragms) or chemical resistance is the prime concern. Fluoroelastomers have excellent resistance to ozone and weathering, oils and most chemicals.
They are, however, very expensive, unsuitable for use with phosphate esters and ketones and have poor low temperature capabilities.
Typical applications include accumulator bladders, diaphragms, gaskets, O-rings and seals operating in especially harsh environments.
Viton® is a registered trade mark of DuPont Performance Elastomers.

|
|
Fluorosilicones can operate over a very wide range of temperatures (-60°C to +200°C) and their resistance to di-ester lubricants, ozone and weathering is excellent. They have good electrical strength and moderate oil resistance.
However, they are particularly expensive rubbers and unsatisfactory for use with phosphate esters. Like Silicone rubbers, their physical properties and permeability to gases are poor.
Typical applications include aerospace fuel system components, diaphragms, gaskets, hose lining, seals and O-rings.

|
|
The properties of Hydrogenated Nitrile Rubber (HNBR) depend upon the acrylonitrile content and the degree of hydrogenation of the butadiene copolymer. They have rather better oil and chemical resistance than Nitrile Rubber and can withstand much higher temperatures. HNBR has excellent resistance to sour oil and gas, steam, hot water and ozone. Physical properties (e.g. tensile and tear strength, elongation, abrasion resistance, compression set, etc.) are also excellent and compounds exhibit good dynamic behaviour at elevated temperatures. Like EPDM , HNBR can either be cured with sulphur or peroxide, depending upon which properties are the most important. Components in HNBR offer an excellent range of performance at a cost between Nitrile rubber and Fluoroelastomers.
Limitations include poor electrical properties, poor flame resistance and attack by aromatic oils and polar organic solvents.
Typical applications include accumulator bladders, diaphragms, gaskets and seals, especially for the oil and gas industries.

|
|
Natural rubber is the only non-synthetic rubber and has been in commercial use since the beginning of the 20th century. It is extracted from the sap of the Hevea Brasiliensis tree grown in renewable plantations. It is fully biodegradable.
Tensile strength, elongation and abrasion resistance is excellent over a wide hardness range, and with the exception of certain formulations of polybutadiene, it has the highest resilience of all rubbers. With its good tear strength, fatigue resistance and excellent compression set it is the ideal choice for dynamic applications at low and ambient temperatures. Weathering resistance is good for black compounds but only fair for white and coloured mixes.
Although natural rubber can be used with water and some dilute acids, alkalis and chemicals, EPDM is normally preferable for most aqueous applications. Natural rubber compounds are not suitable for exposure to petroleum based oils and fuels. It has poor resistance to elevated temperatures and is susceptible to attack by ozone unless specifically compounded with anti-ozonants.
Typical applications include anti-vibration mounts, drive couplings, haul-off pads and tyres.

|
|
Acrylonitrile Butadiene Rubber, usually shortened to Nitrile, was developed in 1941 as the first oil resistant rubber. Grades with high acrylonitrile content have better oil resistance whereas low acrylonitrile content gives better low temperature flexibility and resilience. Nitrile has moderate physical properties but good abrasion resistance. Gas permeability is low.
Ozone resistance and electrical properties are poor. Flame resistance is poor and it is not suitable for use with use with polar solvents (e.g. MEK).
Certain grades can be compounded with PVC to improve ageing, flame, petrol and ozone resistance. Carboxylated grades of Nitrile (XNBR) have improved physical properties and higher temperature resistance. Potable water (WRC/WRAS) compounds are available as well as mixes suitable for use in the food and pharmaceutical industries.
Typical applications include accumulator bladders, diaphragms, gaskets, hose, liners, O-rings and seals.

|
|
Perfluoroelastomers (FFKM) rubbers fill an important niche for applications involving aggressive chemicals at temperatures up to 300°C.
They are extremely expensive and have poor physical properties and limited use at low temperatures.
Typical applications include accumulator bladders, core sleeves, gaskets, O-rings and seals working in extremely harsh environments, particularly within the oil and gas industries.
Kalrez® perfluoroelastomer parts and seals resist over 1,800 different chemicals while offering the high temperature stability of PTFE (327°C). Advanced properties help maintain seal integrity, reduce maintenance and operating costs and improve safety. Kalrez® perfluroelastomer parts provide reliable, long-term service with a wide range of aggressive industrial and electronic grade chemicals. It is used in highly aggressive chemical processing, semiconductor wafer processing, pharmaceutical, oil and gas recovery, and aerospace applications. Production facilities for Kalrez® are ISO 9000 and AS 9100 registered. Kalrez® parts are supplied in standard O-rings or custom shapes .

|
|
The key properties of Polyacrylic (ACM) are its resistance to hot hydraulic oil and oxidation. It is also resistant to ozone and weathering and in these respects it is much superior to Nitrile Rubber.
Water resistance is poor, as is its resistance to acids and alkalis. Low temperature applications are limited to -10°C. Polyacrylic has very low resilience below 70°C and has found use in vibration damping.
Typical applications include automotive transmissions components requiring resistance to hot oil or fuel.

|
|
Chloroprene Rubber (CR), widely known as Neoprene®, was one of the first oil resistant synthetic rubbers. However, it has only moderate resistance to petroleum based oils and fuels. It can be considered as a good general purpose rubber with an excellent balance of physical and chemical properties. It has better chemical, oil, ozone and heat resistance than natural rubber but a rather lower level of physical properties. Chloroprene tends to slowly absorb water and its electrical properties are poor. Its gas permeability is fairly low and flame resistance is excellent, chloroprene being one of the few rubbers that are self-extinguishing. Neoprene gives excellent rubber-metal bonds and good resilience. Certain grades of Neoprene may crystallise and harden during storage although they will thaw on heating.
Chloroprene is widely used because of its wide range of useful properties and reasonable price. Typical applications include belting, coated fabrics, cable jackets, seals and gaiters.
Neoprene® is a registered trademark of DuPont Performance Elastomers.

|
|
Polyurethanes fall into two main classes; polyester (AU) and polyether (EU). These materials have outstanding tensile strength and abrasion resistance. They also have good resistance to oxidation, ozone and petroleum based fuels and oils. Polyesters have physical properties slightly superior to those of polyethers. Electrical properties are fairly good.
Unlike polyethers, polyesters can be affected by hot water and high humidity and their resistance to acids and alkalis is low. Maximum operating temperatures should not significantly exceed ambient. Compression set and creep properties are only fair. In view of the high hysteresis (damping) of most polyurethanes, care must be taken for applications involving high frequency deformation and tyre/wheel speeds of over 8 mph.
As these materials are liquid cast, tooling prices tend to be lower than for heat and pressure moulded rubbers.
Typical applications include abrasion-resistant coatings and linings, diaphragms, gaskets, haul-off pads, hoses, seals and tyres/wheels.

|
|
Silicone Rubbers are ideal for high and low temperature applications. Electrical properties are excellent and resistance to weathering and ozone attack is outstanding.
It is not resistant to super-heated steam. Physical properties are generally low but are at least retained at higher temperatures. Gas permeability is very poor as is resistance to petroleum based fluids. Silicone rubbers are expensive in comparison to most other rubbers.
Food Quality/FDA compliant grades are available for use in the food and pharmaceutical industries. Room Temperature Vulcanisation (RTV) grades are also available, usually for prototypes or small batch quantities.

|
|
Styrene Butadiene Rubber (SBR) is one of the cheaper general purpose rubbers. Its physical strength, resilience and low temperature properties are usually inferior to Natural Rubber though heat-aging properties and abrasion resistance are better.
SBR is not resistant to oil or fuel resistant and it can be prone to weathering.
Typical applications include drive couplings, haul-off pads, shoe soles/heels and car tyres.

|
|
|
|