Enter keywords or manufacturers
|
|
|
|
All Seals Incorporated
The Sealing Specialists
2110 S. Yale Street
Santa Ana, CA 92704
Phone: (714) 556-4931
Fax: (714) 557-3257
|
|
|
|
10-3050
NON-SAG, BUTTER-ON EPOXY COATING |
10-3050 is a thixotropic, Non-Sag, gel epoxy
designed to protect motor windings from abrasives, chemicals,
vibration, oils, jet fuels, etc... 10-3050 self levels to
a smooth void free coating once applied with a spatula or
brush.
10-3050 stays exactly where applied and will not run out
of coil windings or stator slots. This unique adhesive forms
a tenacious bond to most substrates.
10-3050 is color coded to facilitate proper mixing of Resin
and Catalyst. 10-3050 Resin is White and Catalyst is Black.
Typical Specifications |
Mixed viscosity, 25°C, cps |
Paste |
Pot life, 25°C |
40 Minutes |
Color mixed |
Grey |
Specific gravity, 25°C/25°C |
1.4 |
Hardness, shore D |
75D |
Shrinkage linear, in/in |
.002 |
Tensile strength, psi |
8,000 |
Compressive strength, psi |
20,500 |
Water absorption, 240 hrs, 96% rh, % weight grain |
0.8 |
Operating temperature range, °C |
-60 to +160 |
Thermal conductivity, Btu in/ft2 hr °F |
4.1 |
Thermal expansion coefficient, per °C |
49 x 10-6 |
Dielectric strength, volts/mil |
485 |
Dielectric constant, 60 Hz |
0.01 |
Dissipation factor, 60 Hz |
.015 |
Volume resistivity, ohm-cm |
4.0 x 1014 |
|
MP 5405 |
MP 5405 is a two part unfilled
epoxy adhesive designed for ceramics, and most plastics. It
cures to a tough semi-rigid material, and is free flowing
in viscosity. It gives good resistance to water, salt spray,
inorganic acids and bases, and most organic solvents. It was
especially formulated to a 1:1 mix ratio for use in either
MMD equipment or side-by-side dual cartridges for easy dispensing.
A handling cure is normally achieved at room temperature
within 20 - 30 minutes with full cure in 24 hours. An elevated
temperature cure schedule can be used to reach final properties
quickly.
Handling and Storage:
- 1) Bring both components to room temperature prior to
mixing. Mix 1 parts A to 1 part B thoroughly.
- Allow to cure undisturbed until product is fully gelled
or tack-free to the touch.
- Clean up uncured resin with suitable organic solventsuch
as MEK, acetone or a chlorinated.solvent.
Mix Ratio: 1A:1B by weight or 1A:1B by volume.
Shelf Life: 12 Months |
MP 54750
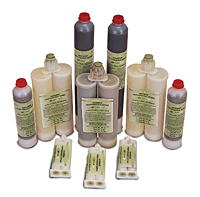
|
MP 54750 is a two part unfilled
epoxy structural adhesive designed for bonding application
requiring conformance to the Code of Federal Regulations Title
21 175.105 (Adhesives) and 175.300 (Resinous and polymeric
coatings)1. It cures completely at room temperature to a tough,
semi-rigid polymer. It has good wetting and adhesion to most
surfaces and has a free flowing viscosity. It has very good
resistance to water, acids and bases and most organic solvents.
It was especially formulated to a 1A:1B volume mix ratio
for use in side-by-side dispensing cartridges and meter/mix
and dispense equipment. MP 54750 will reach full cure at room
temperature within 24 –48 hours. Cure time can be accelerated
by the application of heat. Times and temperatures from 2
hours at 150F to 10 minutes at 225F are typical for most applications.
Time to heat substrate must be taken into account. Cooler
temperatures will also extend work time and increase cure
times. |
MP 54190 |
MP 54190 is a two part mineral
filled epoxy adhesive designed for bonding metals and plastics.
It cures at room temperature to a tough, semi-flexible material.
It has good wetting to most surfaces and is free flowing to
penetrate cavities and give good self leveling and air release.
This product gives very good vibration and impact resistance.
It gives good resistance to water, salt spray, inorganic acids
and bases and most organic solvents.
It was especially formulated to a 1A:1B volume mix ratio
for use in side-by-side dispensing cartridges and meter/mix
and dispense equipment. MP 54190 will reach handle cure at
room temperature within 16 – 24 hours. Cure time can
be accelerated by the application of heat. Times and temperatures
from 2 hours at 65°C to 20 minutes at 100°C are typical
for most applications. Time to heat substrate must be taken
into account. Cooler temperatures will also extend work time
and increase cure times. |
Scotch-Weld™
Epoxy Adhesive
2216 B/A Gray • 2216 B/A Tan NS • 2216 B/A Translucent |
3M™ Scotch-Weld™
Epoxy Adhesive 2216 B/A Gray, Tan NS and Translucent are flexible,
two-part, room temperature curing epoxies with high peel and
shear strengths.
Advantages
- Excellent for bonding many metals, woods, plastics, rubbers,
and masonry products.
- Base and Accelerator are contrasting colors.
- Good retention of strength after environmental aging.
- Resistant to extreme shock, vibration, and flexing.
- Excellent for cryogenic bonding applications.
- 2216 B/A Gray Adhesive meets MIL-A-82720 and DOD-A-82720.
- 2216 B/A Tan NS Adhesive is non-sag for greater bondline
control.
- 2216 B/A Translucent can be injected.
|
|
|